2021 CFIA Feed Production Technology School addresses industry issues
Participants represented both commercial and integrated facilities as well as the allied industry including ingredient, equipment, and service providers.
November 27, 2021
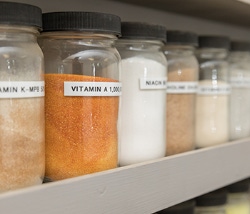
By ADAM FAHRENHOLZ, CHARLES STARK AND WILMER PACHECO
One of the best things about working in the education and outreach areas of the animal food arena is the opportunity to interact directly with the industry in “continuing education” efforts. In this space in the past, we’ve shared with you a number of these activities, including distance education and resource development pursuits. But our favorites of these industry interactions tend to be those where we get to meet with everyone in person, and when we get to do some learning ourselves.
On November 17th, the Carolina Feed Industry Association (CFIA) and NC State University held the 44th Annual Feed Production Technology School. Though “annual” is in the name, the meeting had only been held once since 2017, with both hurricanes and COVID-19 playing their roles in canceling the event. But absence makes the heart grow fonder, and this year’s participation was quite strong with over 80 individuals attending. Participants represented both commercial and integrated facilities as well as the allied industry including ingredient, equipment, and service providers.
One of the primary goals of this meeting is to allow the industry to both help set the topic list and do a fair amount of the sharing. With this in mind, there was an excellent variety of subjects and interactive discussions throughout the day.
As usual, the Production School kicked off with an update from NC State regarding current academic, extension and research activities. Students receiving scholarships from CFIA were recognized, and a short discussion was held about potential future efforts related to both program and infrastructure advancements. Marissa Cohen, Area Specialized Agent for Animal Food Safety, shared information regarding training opportunities and ongoing resource development for regulatory compliance assistance. The group was also introduced to some of the newly developed teaching tools, including augmented-reality equipment, virtual tours, and web-based laboratory simulations that have been developed to assist with distance education coursework.
Gary Huddleston with the American Feed Industry Association (AFIA) spoke to participants about current and upcoming OSHA safety regulations. Gary spoke on a number of applicable OSHA standards, including working surfaces and fall protection, emergency planning, hazardous materials and hazard communication, PPE, and electrical and fire protection, among others. The final part of the presentation, which included discussion with the participants, focused on planned OSHA actions related to COVID-19 mitigation and vaccine mandates, including the impacts of company size, paid time off implications, and the need for written plans. While some requirements were written with an early December implementation date in mind, legal challenges are being presented, and so AFIA recommends all facilities become familiar with any proposed and/or finalized federal or state plans that might affect their operations.
Chandler Adams (Chandler Adams, LLC) presented a detailed walkthrough in pictures of the newly constructed Mountaire feed mill in Maxton, NC. A “virtual tour” of new construction or significant renovation is always a part of the school, and tends to be a favorite of participants, since many don’t ever get the opportunity to travel and see other facilities or the new technologies that are being implemented.
Jamie Smith with CPM Beta-Raven spoke on viruses and ransomware as they can potentially impact automation control systems. Some of the information he shared are things we should all be aware of, such as being aware of opening emails and especially attachments from unknown senders or those that have been intentionally made to look like a legitimate contact by changing just a few letters or symbols. From an automation perspective, Jamie shared that prevention is key, including keeping systems isolated from other networks when possible and moving towards virtual environments with constant backups and updates so that if the primary system is attacked the backup is ready to be put into service.
Lunch was North Carolina barbecue, outside under a tent on a sunny, 70-degree fall afternoon. Enough said.
The afternoon session was led off by Stacy Sereno, State Legislative Director and Legislative Counsel for the North Carolina Farm Bureau Federation. She spoke to the group about a number of legislative issues impacting the state, including updates to existing laws and regulations, nuisance lawsuits and budgets as they might affect infrastructure and development grants. She also covered information on current and proposed statewide plans for preventing and dealing with foreign animal diseases, most notably African Swine Fever.
Adam Downes, Director of Feed Ingredient Purchasing with Mountaire, provided an ingredient market update and led a discussion on the pressures facing both ingredient costs and logistics. Supply chain difficulties and labor shortages were, as expected, a significant source of frustration around the room. Adam also took some time to tie together ingredient prices, alternative markets (e.g., ethanol) and energy costs to give participants an idea of the bigger picture of what is currently, and is likely to be in the future, causing pressures on supply and demand. Lastly, due to both trucking and rail issues, the conversation turned to expectations for larger holding and warehousing capacity needs in order to prevent ingredient restrictions due to supply interruptions.
Edgar Miller, General Manager, Truck Enterprises (ret.) has been an invited speaker at past Production Schools and was once again asked to address labor management in the agricultural workplace. He provided statistics and reasoning behind the recently coined “Great Resignation” and spoke on the drivers behind current workplace culture and both employee and employer expectations. Overall, the focus was on a change in leadership requirements to focus on development and purpose and to have empathy for employees and their evolving working environment viewpoints relative to generations passed.
Finally, James Neal, Regional Operations Manager with Smithfield Foods, shared updates on new feed mill technologies being implemented in batching, pelleting and cooling, post pellet liquid application and general infrastructure. He also stressed the importance of knowing your equipment suppliers and neighboring facilities with similar equipment in order to mitigate issues with parts and labor availability. This presentation served as the beginning of the “open forum,” an informal discussion where anyone from the group of participants could introduce a topic or an issue of concern and solicit feedback from their peers on shared experiences and hopefully find some solutions.
Overall, the topic list and general theme of the CFIA/NC State Feed Production Technology School changes from year to year. But it always remains a highlighted date on the calendar when feed producers, allied industry and academia get to come together, learn from one another, and simply share the company of other folks dedicated to this industry we love.
You May Also Like