thumbnail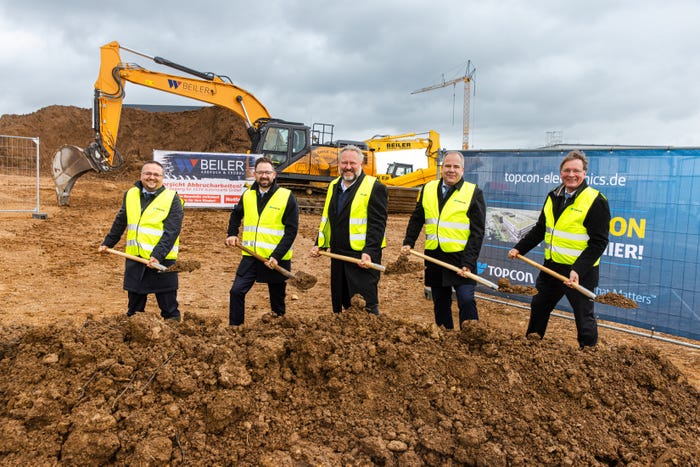
Agribusiness News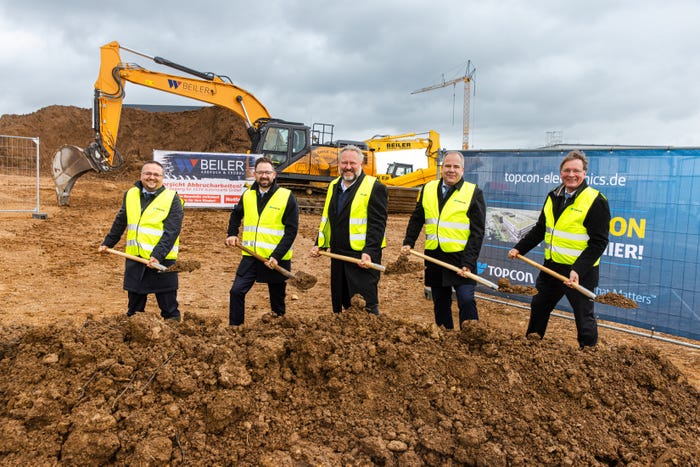
Topcon announces plans for new state-of-the-art manufacturing facility in GermanyTopcon announces plans for new state-of-the-art manufacturing facility in Germany
Topcon Positioning Systems has announced a new manufacturing facility will be built in Geisenheim, Germany for the company’s Topcon Electronics operation.
Subscribe to Our Newsletters
Feedstuffs is the news source for animal agriculture